На счету филиала «Торфобрикетный завод «Сергеевичское», структурного подразделения УП «МИНГАЗ», отметившего свое 55-летие, заслуг немало. Оно ежегодно удостаивается наград, указывающих на высокое качество налаженного производства, а его сотрудники поощряются за профессионализм и личный вклад в работу всегда достойно принимающего вызовы времени завода. Вот и совсем недавно автоматизация технологического процесса брикетного цеха и котельной филиала ТБЗ «Сергеевичское» принесла УП «МИНГАЗ» диплом победителя V республиканского конкурса на соискание премии по энергоэффективности «Лидер энергоэффективности Республики Беларусь – 2019».
Эдуард Геннадьевич Гаврилкович,
генеральный директор РУПП «Гранит»
С чего же и когда начиналось становление одного из лучших торфопредприятий Беларуси, какие цели и задачи перед ним изначально ставились? История его, действительно, непростая. Стоит отметить, что торфяная промышленность на территории Беларуси была создана более 100 лет назад. Впервые в промышленных масштабах торф начали разрабатывать еще в конце XIX века. До 1960 года он в стране оставался основным видом топлива, на котором работало большинство электростанций. Решение о создании предприятия «Сергеевичское» принято в конце 1963 года. Это было вызвано необходимостью обеспечения фрезерным торфом ТЭЦ республики, сельского хозяйства и снабжения бытовым топливом населения.
Строительство первой очереди начиналось в 1965 году на чистом месте, среди болот и сотен гектаров торфяных залежей. Сырьевой базой торфопредприятия «Сергеевичское» явились торфомассивы «Ореховский Мох», «Рады-Голышевка», «Гала-Ковалевское». Добытый торф поступал в качестве топлива на Жодинскую и Светлогорскую электростанции. Одновременно велись работы по строительству торфобрикетного завода, прокладке железнодорожных путей узкой колеи.
Строительство жилья и социальных объектов шло темпами, опережающими ввод и эксплуатацию производственных мощностей. Это способствовало закреплению кадров на заводе. В жилищном поселке были построены детский сад и ясли, больница, клуб, гостиница, столовая и т.д.
О расширении с годами возможностей предприятия, о сегодняшнем дне и планах развития мы говорим с генеральным директором УП «МИНГАЗ» Вадимом Евгеньевичем ШОЛОНИКОМ.
– Вадим Евгеньевич! Насколько быстро росло производство на предприятии в первые десятилетия после его основания?
– Со строительством брикетного завода в 1968 году наладилось стабильное производство топливных брикетов. И уже вскоре, в 1974 году, были пересмотрены перспективы развития предприятия. Тогда объемы добычи топливного торфа составили 800-900 тыс. т, а производство топливных брикетов – 60 тыс. т.
В период 1979-1981 годов произведена реконструкция брикетного цеха. Объем производства топливных брикетов увеличился до 100 тыс. т в год. В конце 1980-х годов были достигнуты самые высокие темпы роста производства топливных брикетов – 122,7 тыс. т в год.
В 1985 году торфопредприятие «Сергеевичское» переименовано в производственное торфобрикетное объединение «Сергеевичское». Почти сразу же, в 1986 году, в состав предприятия вошел участок «16 Красных партизан», который до 1991 года осуществлял добычу торфа и производил топливные брикеты.
В 2000 году заработала Программа поддержания торфопредприятий Республики Беларусь. Сергеевичский завод ожил и начал развиваться, особенно после того как был реорганизован путем присоединения к производственному республиканскому унитарному предприятию «МИНГАЗ» в 2015 году. Отмечу, что на момент присоединения износ основных средств на предприятии составлял 90%!
– Значит, Вадим Евгеньевич, остались в прошлом тяжелые проблемы с дефицитом сырья, заказчиками, современным оборудованием?
– В целом, верно. Работа наладилась, и в завтрашний день смотрим с оправданным оптимизмом. Потому что теперь сырьем для производства топливных брикетов себя обеспечивает сам филиал. Добыча торфа ведется на месторождении «Гала-Ковалевское». Предприятие обеспечено необходимым технологическим оборудованием для производства болотно-подготовительных работ и добычи торфа. По состоянию на 1 января 2022 года за филиалом «Торфобрикетный завод «Сергеевичское» числятся 888 га земель, из которых: 371,7 га – действующих площадей для добычи торфа; 154,8 га – резервных площадей в стадии строительства. Запасы торфа на отведенных площадях оцениваются в 1293 тыс. т.
Запасы торфа по всем перспективным месторождениям составляют 11 593,9 тыс. т торфа. Здесь надо отметить, что при ежегодном производстве топливных брикетов в объеме 80 тыс. т обеспеченность сырьем брикетного завода составит 70 лет!
Централизованная доставка топливных брикетов потребителям производится автомобильным и железнодорожным транспортом самого предприятия. Подвоз торфа с площадей добычи к цеху переработки осуществляется железнодорожным транспортом. Среднее расстояние доставки торфа с полей к брикетному цеху составляет 15 км.
– А какими новыми возможностями по переработке сырья располагает предприятие?
– Многими! Например, внедрение автоматизированной системы управления технологическим процессом производства топливных брикетов в филиале «ТБЗ «Сергеевичское» УП «МИНГАЗ» позволило:
• задавать основные качественные характеристики выпускаемой продукции (влагу, золу) и изменить их в зависимости от требований, предъявляемых потребителями торфяного топлива;
• повысить качество выпускаемой продукции за счет увеличения теплотворной способности торфяного топлива в среднем на 17%;
• снизить удельные расходы энергоносителей – расход тепловой и электрической энергии, расход торфа на тонну произведенной продукции;
• снизить количество внеплановых ремонтов;
• начать планировать закупку запчастей и материалов;
• контролировать количество произведенной продукции за час, день, смену и т.д.;
• вести учет количества поступающего сырья, используемого для производства брикетов и выработки пара на технологию и отопления жилого фонда поселка;
• себестоимость на протяжении 5 лет не менять;
• определять наработку количества часов для основного технологического оборудования, что позволяет не производить техническое обслуживание и капитальный ремонт оборудования, не выработавшего свой ресурс, и прогнозировать графики ремонтных работ.
Здесь очень важно, что все управление технологическим процессом возможно в дистанционном – автоматическом режиме и в местном – ручном. Дистанционный режим работы может быть полностью автоматическим (система сама выбирает оптимальный режим работы), а также существует возможность ручной регулировки параметров работы технологического оборудования, когда параметры задаются с персонального компьютера, установленного на рабочем месте оператора.
Возможность просмотра и анализа удельных расходов тепловой и электрической энергии на тонну производимой продукции позволяет анализировать и оптимизировать расходы энергоносителей в зависимости от характеристик поступающего сырья, определить эффективность принятых персоналом действий в случаях ручной корректировки работы системы автоматического управления.
Следует отметить: сегодня учет изготовленной продукции осуществляется автоматически при помощи бесконтактных щелевых датчиков. Системой формируются отчет и схематический график о количестве изготовленной продукции на каждую единицу прессового оборудования с возможностью вывода на печать. Учет поступающего сырья происходит при помощи тензометрических весов на конвейерных лентах. Так система формирует отчет. Для удобства информация об изготовленной продукции, поступающем сырье и затратах энергоносителей на изготовление тонны продукции сводится в таблицу.
– Замечательно. Только эти новейшие технологии требуют заботы специалистов…
– Конечно! Высококлассные специалисты на предприятии есть. Контроль наработки часов оборудования позволяет осуществлять планирование и проведение своевременного технического обслуживания. Система заблаговременно предупреждает о необходимости проведения технического обслуживания или текущего ремонта каждой единицы оборудования, выводит информацию о наработке часов в виде таблицы и графика.
Еще существует возможность оперативного контроля работы оборудования с выдачей информации об его неисправности. Так, токовые нагрузки на электрические двигатели технологического оборудования, оформленные в виде мнемосхемы, позволяют в режиме реального времени контролировать нагрузку на каждый элемент технологической цепочки, предупреждают об его перегрузке или авариях. А мгновенный расход электрической энергии позволяет контролировать эффективность работы всего оборудования. Таким образом, экономия топливно-энергетических ресурсов достигается за счет недопущения работы оборудования в неоптимальных режимах.
Словом, примененные при реконструкции предприятия решения по автоматизации выпуска продукции обеспечили работу оборудования в диапазоне максимальной эффективности и производительности!
– Белорусский и зарубежный потребители давно отмечают приемлемые цены и высокое качество вашей продукции. Чем это обусловлено, каким образом отслеживается, гарантируется?
– Контроль за всем оборудованием, в т.ч. учет наработки часов и фиксация отказов и внештатной работы, обеспечил своевременное и качественное выполнение технического обслуживания, текущего ремонта. Совокупность положительных эффектов от внедрения систем автоматического регулирования позволила сократить себестоимость, повысить культуру производства и обеспечить постоянство качества выпускаемой продукции, которое отслеживает производственно-технический отдел на всех этапах производства. Проверке подвергается все: от добытого сырья до готового брикета.
Конечно же, контроль качества продукции проводится и в нашей испытательной лаборатории. В ходе разноплановых испытаний проверяются показатели зольности, влажности, теплоемкости, механической прочности и радиоактивности.
– И в заключение, Вадим Евгеньевич, расскажите, пожалуйста, о ваших традиционных и новых деловых партнерах. Под какой торговой маркой отправляется на рынок продукция предприятия, какие у него свежие идеи по расширению своего присутствия на нем?
– Если коротко, то эти вопросы обстоят следующим образом.
Топливные брикеты производятся на ТБЗ и поставляются на рынок под двумя марками – БТ-1 и БТ-2.
Основными потребителями топливных брикетов стали цементные заводы Могилевской области, топливоснабжающие предприятия Минской области. Также предприятие реализует торф для компостирования сельскохозяйственным организациям и УП «Минскзеленстрой». Топливные брикеты поставляем и за рубеж, в основном в Украину.
Добытый филиалом торф используется не только как сырье для производства брикетов, но и еще как топливо для получения тепловой энергии в котельной предприятия, которая на данное время оснащена наиболее современным оборудованием в Беларуси. Полученная в котельной тепловая энергия идет для обогрева поселка Правдинский и объектов на его территории.
Что касается расширения ассортимента продукции – есть планы! Скажем, сегодня торф, добытый нашим заводом, охотно используют для приготовления компостов организации сельского хозяйства и физические лица. Проект по созданию питательного и растительного грунта на базе торфа только начинает развиваться. В 2023 году планируется организовать линию по производству данного вида продукции. При низкой себестоимости она довольно востребована на рынке. И вообще, филиал «ТБЗ «Сергеевичское» УП «МИНГАЗ» всегда открыт для ярких идей, взаимовыгодного делового сотрудничества!
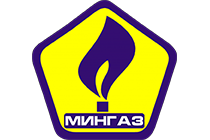
Филиал «Торфобрикетный завод «Сергеевичское» УП «Мингаз»
Ул. Юбилейная, 46,
222839, пос. Правдинский,
Пуховичский р-н, Минская обл.,
Республика Беларусь
Приемная: (+375 1713) 42-751
Специалист по маркетингу: (+375 1713) 21-459; (+375 29) 124-68-70
E-mail: torf_007@mail.ru